What is an Electrical Drive? Types, Advantages, Disadv
An electrical drive is defined as an electronic device designed to control certain parameters of the motor for controlling the electrical energy into mechanical power in a precise controllable way.
Table of contents
Electrical power systems employed for motion control are called “Electrical Drives”.
It consists of a sophisticated electronic system or a combination of different systems for the purpose of motion control.
Motion is provided with the help of prime movers.
Example of prime movers are Petrol engines, Diesel engines, gas or steam turbines, steam engines, hydraulic motors, and electric motors.
Drives power systems employing electric motors are known as electric drives.
Block Diagram of Electrical Drive
A modern electrical drive capable of variable controlled speed is made of some important parts as shown in the below block diagram.
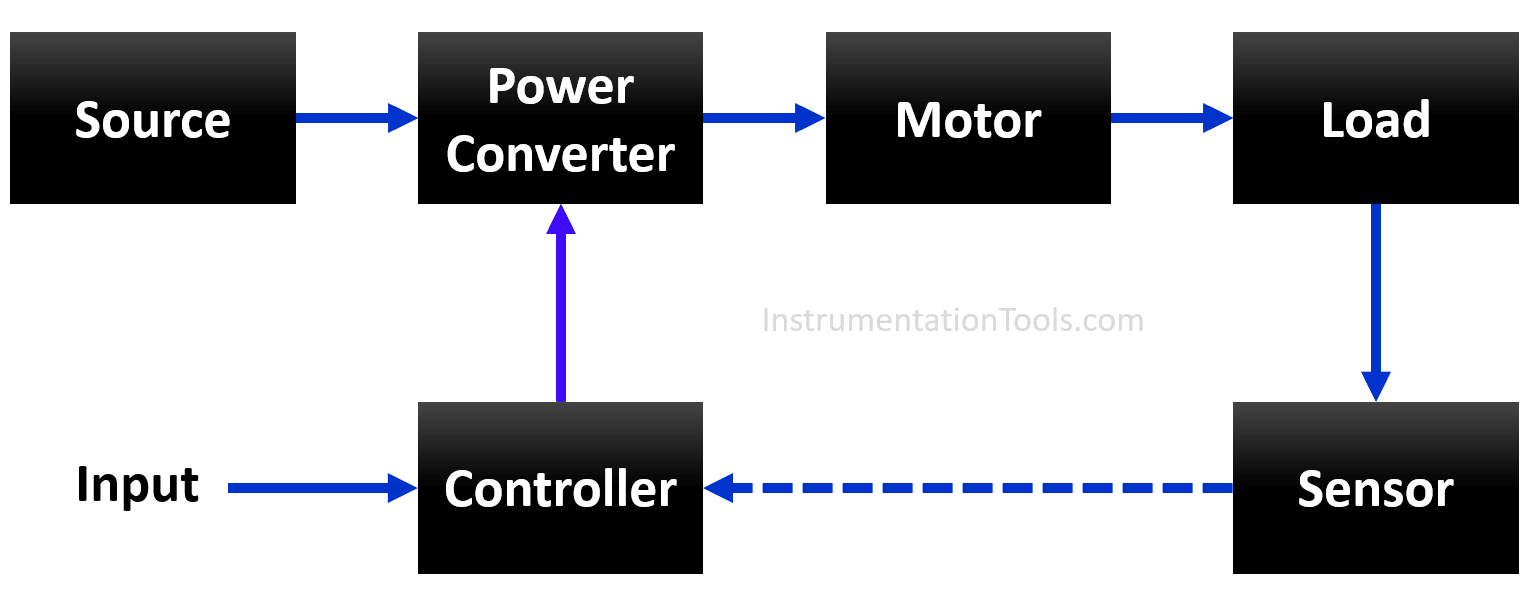
Source: Source can be DC or AC source.
Power converter: AC to DC, AC to AC, DC to DC, DC to AC converters.
Motor: Converts electrical energy in to mechanical energy, it is the heart of the electrical system.
Commonly used motors are
- DC motors – series, shunt/parallel DC motor, compound and permanent magnet DC motor.
- Induction motors – wound rotor and linear, squirrel cage.
- Brush less dc motors
- Stepper motors.
Load: It can be a machine to accomplish a given task. Example is Pump, Fan, Machine tools.
Controller: The power required for the motor is supplied by the controller.
Sensor: Depending upon the type of control required, various inputs from sensors are taken. An example is a speed, current.
Types of Electrical Drives
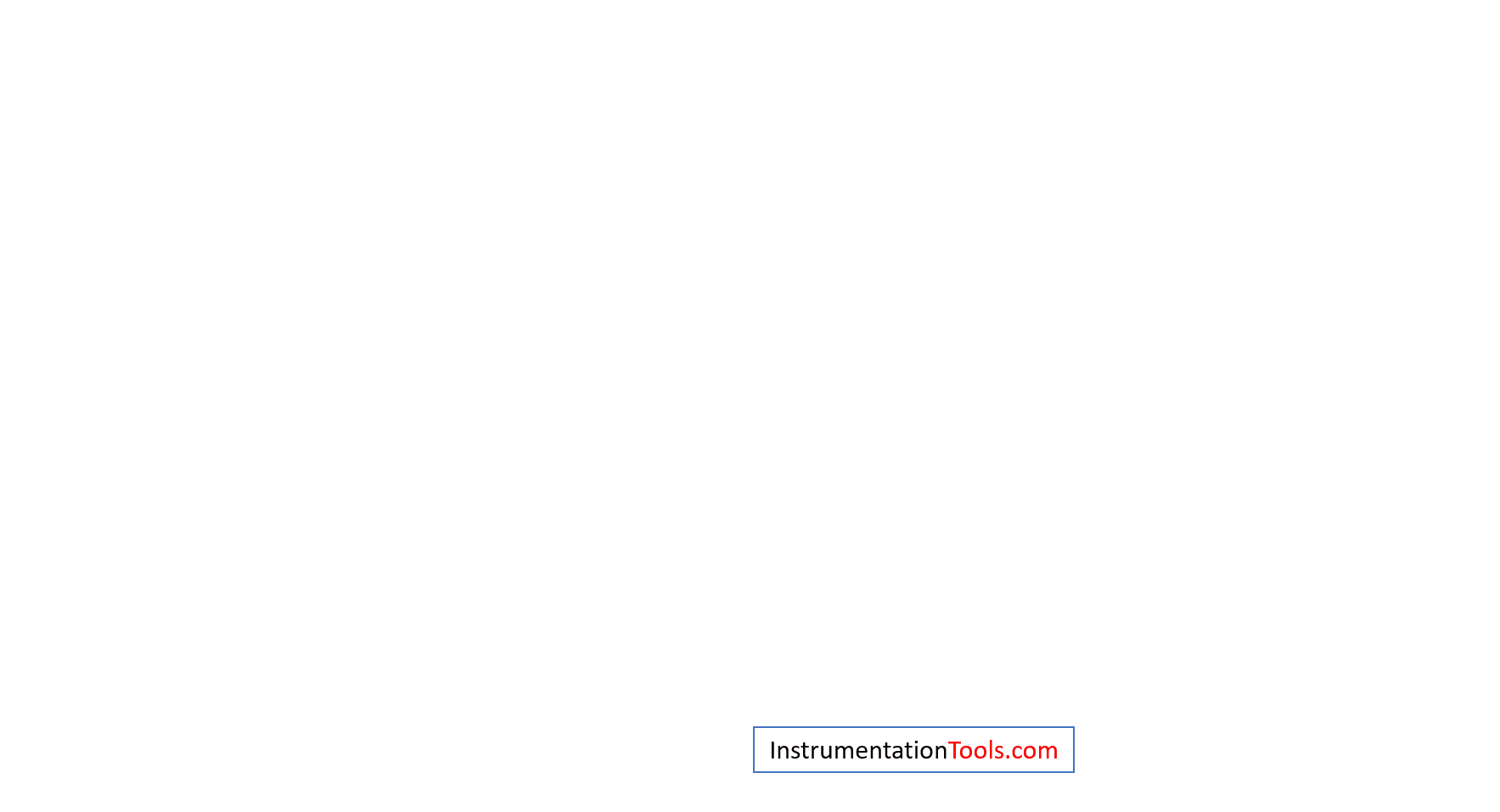
Based on Supply
There are two types available in this category. They are
AC Motor drives
AC drive is a device used to control the speed of an electric motor such as a three-phase induction motor by changing the frequency of the electrical supply to the motor.
AC drive is also called Variable Frequency Drive (VFD) or Variable Speed Drive (VSD).
DC Motor drives
It is basically speed control system of a DC electrical motor that supplies voltage to the motor to operate at desired speed.
DC drives are classified as analog DC drives and digital DC drives.
Digital DC drive can offer precision control.
Based on Number of Motors
There are three types available in this category. They are
Individual
There will be a separate drive motor for various parts of a machine.
Example: Lathe machine.
Multi Motor
Separate motors are provided for actuating different parts of a machine.
Example: Cranes.
Group Drive
In a group drive, one motor is used as a drive for two or several machines.
The motor is connected by a single shaft, other machines are connected to the shaft by belts and pulleys.
Group drive is most economical.
Based on Speed
There are two types available in this category. They are
Constant Speed drive
Machine tools require more or less constant speed drives, squirrel cage induction motor along with the manual controls are used.
Variable Speed drive
The main purpose of variable speed drive is to control speed along with acceleration, deceleration, torque and finally the direction of machine.
They are used to reduce power consumption.
Based on Control Parameters
There are three types available in this category. They are
Vector Control Drive
Vector control is most accurate than any other kind of variable frequency drive (VFD).
In this control mode, torque and speed controlled using pulse width modulation (PWM) techniques in an inverter.
These are used for AC synchronous and induction motors.
Constant Power Drive
When a motor while carrying rated current in its armature provides constant power at all speeds in a certain range of speed control it is known as constant power drive in that range of speed control.
Constant Torque Drive
Constant torque load type drive is distinctive when fixed volumes are being handled.
Examples are screw compressors, feeders, and conveyors.
Advantages of Electrical Drives
- Enough overload capacity without loss of life of machine.
- Four quadrant operation.
- Modifiable torque-speed characteristics.
- No requirement of warming up period.
- Higher efficiency.
- Easy control.
- Clean operation, no pollution.
- Wide range of speed control.
- They have flexible control characteristics.
- Electric braking can be employed
- Electric drives can be provided with automatic fault detection systems.
- Electric motors have long life lower noise, lower maintenance requirements and cleaner operation
- Adoptable to almost an operating conditions such as explosive and radio active, submerged in liquids etc.
- They can be started instantly and immediately can be fully loaded.
Disadvantages of Electrical Drives
- High initial cost due to the presence of power converters and controller electronics.
- Regular maintenance and high attention are required.
Applications of Electrical Drives
Extensively used in
- Industrial production,
- manufacturing, and
- process control.
References:
- Electrical Machines by S.N Ali.
- Electric drives by Kothari D.P Rakesh Singh Lodhi.
No comments:
Post a Comment