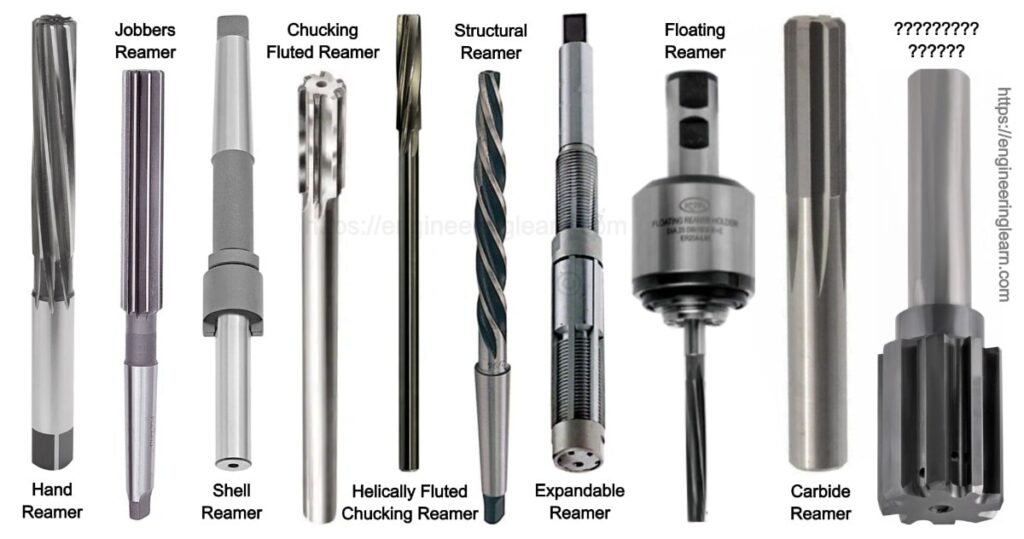
Types of Reamers :- Reamer refers to as a rotary cutting tool which is used to enlarge or finish the product with accurate dimensions. The tool is usually equipped with two or more than two peripheral grooves which might be parallel to the axis or in a right or left-hand helix. Latter produces a better finish as it has a smooth shear cutting which helps to give an accurate finishing. The flutes present on the reamer body act as cutting teeth as well as grooves which helps in accommodating the removed chips.
The reamer is available in various sizes which is specified according to the diameter which is taken across the two margins from the cutting edge, on the diametric line. Reamers are usually made from high carbon steel, HSS, cast alloys cutting material and cemented carbide forms. One should also know that there are various forms in which they are made. For example, these can be solid blade type, adjustable or non-adjustable type, designed for manual operation or for machine operations.
Types of Reamers
Once you know the basics of the reamers, then you must know the type of reamers which helps in selecting the best reamer according to the site requirement. Scroll down to learn more about the types of reamers
1. Hand Reamer
Hand reamers are classified as fluted or rose reamers which have a slight taper on the cutting end to ease entering inside the hole properly. These reamers may be solid or expandable reamers, but the expansion is limited to a certain level. The blades are usually placed irregularly around the body of the reamer. It is placed in such a manner to reduce the tendency to chatter, which a reamer has due to slippage or torsion.
Usually machine reamers includes a chamfer of 45° on the cutting end and are usually used in turret lathes and screw machines. These are also classified as fluted or rose type. Fluted reamers work on the principal of cutting on the chamfer and have radial clearance to a margin of 0.2mm to 0.4 mm in terms of width to assure free and proper cutting.
Reamers Designs
Reamers are designed in a very wide range of sizes accompanied with number of flutes which vary from 3 mm to 16mm in terms of diameter. It is important to know that number of flutes are usually even and while designing it, a sufficient gap should be kept which could accommodate its width and depth to accommodate the chips while cutting. The lands should be large enough to prevent the deflection back from the cutting edges of sufficiently large sections to contain metal that dissipate the generated heat at the cutting edges adequately.
Reamers are classified into two types either hand type or machine type. Other than this reamers can be cylindrical as well as tapered, depending upon the form of the hole to be made on the required site. Reamers are found having 6 to 16 flutes usually, with an irregular spacing along the circle for the good quality of reamed holes.
2. Jobbers Reamer
Jobber reamers are quite similar to that of a hand reamer, the only difference which is found is that these include taper shanks as well as a chamfer of 45° on the cutting end to permit easy and accurate machine use.
3. Shell Reamer
Shell reamers are mounted on special arbors which are made to fit using the driving pins for proper machine use. These are designed mainly for free cutting material and well finished reaming holes to the desired size. The application of such reamers are in drill presses, lathes, automatic screw machines etc.
4. Chucking Fluted Reamer
Chucking Fluted Reamers are intended to freely cut the material and to finish the reaming holes of the required size. These application of such reamers are in drill presses, lathes, automatic screw machines, etc.
5. Helically Fluted Chucking Reamer
Helically Fluted Chucking Reamers have right hand flutes which are especially designed to accomplish the shear cut to produce smooth, true and precise holes in the stainless steels and materials having the hardness ranging from 200-400. These reamers have the tendency of spoiling the soft materials with their heavy working property.
6. Structural Reamer
Structural Reamers include Morse taper shanks which are intended specifically for machine use only. These reamers are commonly used in ships and bridge building where the steel plates punched or drilled holes in them. Even if they are undersize and rough it holds them when assembled properly, to obtain alignment and proper size for admitting bolts or rivets.
7. Expandable Reamer
Expandable Reamers are most commonly used to produce holes of different diameters over a limited range. These reamers lack the rigidity of solid and are frequently used for removing small amount of material.
8. Carbide Reamer
Carbide reamers are used at places which are highly resistant to abrasion, intending to give a longer tool life and excellent finish. These reamers are operated 1.5 times the speed of H.S.S reamers.
Solid carbide reamers create a perfect hole around its own axis, instead of disturbing previously drilled hole. The reamers with large size are made with tips of carbide which are either brazed body or held on the steel body.
9. Floating Reamer
Floating Reamers are used to correct the wrong alignment between the axis of the reamer and the already drilled hole. These reamers have two replaceable and adjustable cutting edges which are together held in one slot of the reamer and allowed to float in the radial direction. These reamers can specifically be used only with rotating work piece on turret lathes.
Feeds and Speed
A good practice suggests that reamers should be operated at a slower speeds as slow speed affects the productivity and high speed causes the material to clutch to the edges and lands of the reamer, resulting in dulling of the edges and holes. Also it should be noted that highly fine feeds are responsible for causing excessive wear due to reamer cut whereas high coarse feeds tend to produce spiral marks or wavy finish.
No comments:
Post a Comment