Types of Check Valve: Function & Application
What is Check Valve?
Types of Check Valve: Function & Applications :- A check valve is a mechanical device which allows the fluid to flow only in one direction. As, the direction of fluid flow is changed, the valve closes the passage for fluid to flow. It is also known as non-return valves or one way-valves. It is generally installed in fluid pipeline to prevent the backflow of the fluid.
The check valves, generally, are two port valves, which means it has one inlet port and one outlet port. The figure 1 shows typical check valve. The first check valve in history was designed and developed by an engineer named Frank P. Cotter in 1907. After this, Nikola Tesla developed a ground breaking check valve which does not have any moving part, see figure 2. This valve is also known as tesla valve.
Function of Check Valve
The working of the check valve mainly depends upon the pressure difference between outlet and inlet port. When the pressure at inlet side is high, the valve opens the passage for fluid to flow. As, the flow reversed, the pressure at the outlet port becomes higher than that of inlet port, the valve closes its passage and flow is blocked. These valves do not require any actuating mechanism, human etc. to operate the valve.
Check valves are generally installed in the operation where backflow of fluid may cause damage to the system and make it inoperative. For instance; the pipelines of sewage systems contain check valve so that the waste can only leave the system not re-enter into the system or in reverse osmosis process the fluid need to pass the system only in one direction, so to ensure this the check valve is installed in the flow line.
To understand the valve selection and installation, one should must know three things; cracking pressure, resealing pressure and valve orientation. The cracking pressure is the minimum pressure at the inlet port that opens the passage, even slightly. The resealing pressure is the minimum pressure at outlet port of the valve that completely seals the valve to prevent the backflow of fluid. And, most importantly, the valve should be installed according to the flow direction, so before installation the ensurity of valve’s operative direction is recommended.
Types of Check Valves
1. Spring Loaded in-line Check Valve: ( Types of Check Valves )
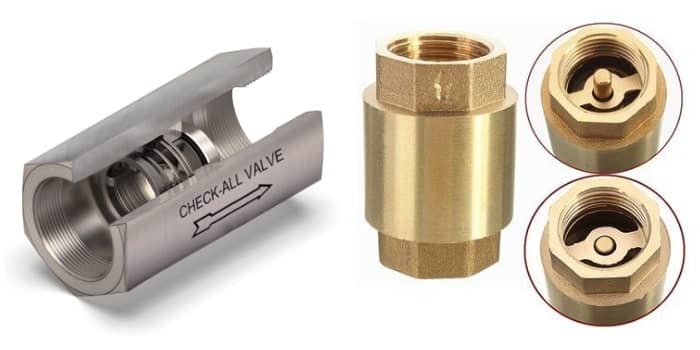
These valves are easy to operate, maintain and have simple design, see figure 3. Where, A is valve body, B is disc, C is spring and D is guide. As, the pressure at the inlet side of the valve exceeds the cracking pressure, the disc gets pushed that creates an opening and the fluid is allowed to flow through the valve. If the pressure at inlet decreased below the cracking pressure or the pressure at outlet exceeds the resealing pressure, the disc moves in reversed path by the help of spring force and closes the opening to prevent the backflow of the fluid. This valve is also design to take care of the pressure surge in the pipeline therefore it also safeguards the pipeline from hammering effect.
2. Spring Loaded Y Check Valve: ( Types of Check Valves )
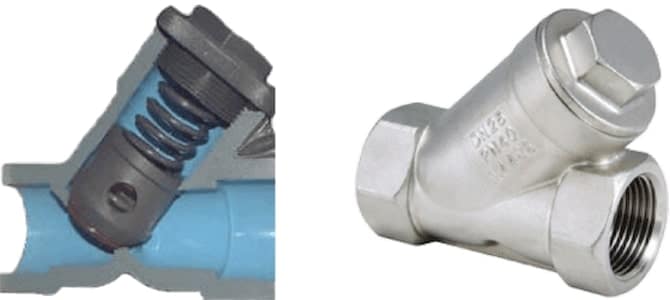
The figure 4 shows the typical illustration of spring-loaded Y check valve. Its operation is similar to the in-line check valve but there is only one difference, that is the disc is placed at an angle to the fluid flow direction. This change enables the check valve to inspect and maintain while the valve connected to the pipeline. But, because of its shape, it takes more space than the in-line valve.
3. Ball Check Valve: ( Types of Check Valves )
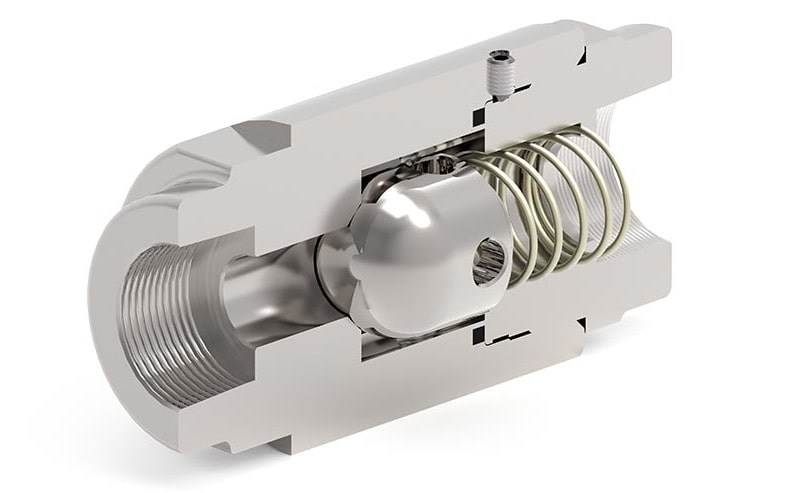
The ball check valve either be spring loaded or free-floating type. As the cracking pressure for spring loaded valve is more than that of free-floating ball valve. Thus, the free-floating type is used for low pressure application and the spring-loaded type is used for high pressure application. The figure 5 shows illustrations of spring-loaded ball check valves. Its working principle is also similar to the in-line check valve, but instead of disc, a ball is used for the purpose.
4. Diaphragm Check Valve: ( Types of Check Valves )
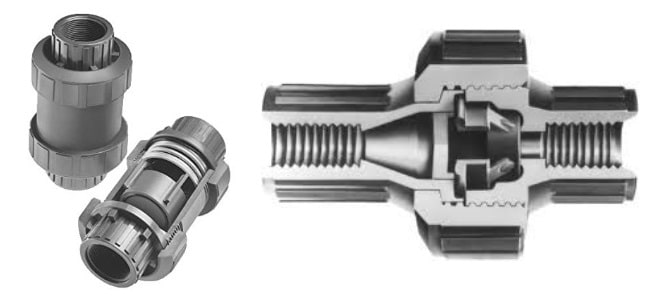
It consists of a rubber diaphragm that flexes inside the valve to open or close the passage. The figure 6 shows schematic diagram of a diaphragm check valve. Because of the diaphragm, there is very low or no cracking pressure possessed by the valve. As the pressure at inlet increases the diaphragm flexes more and the size of passage increases accordingly. In case of any backflow, the diaphragm is forced against the opening and seal the passage to prevent backflow. These kind of check valves are ideal for low pressure or vacuum application.
5. Lift Check Valve: ( Types of Check Valves )
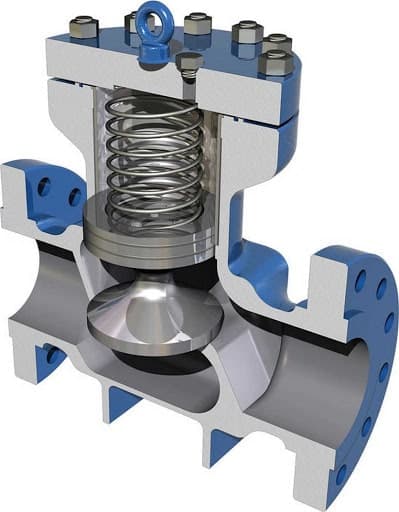
It consists of a spring-loaded disc that lifts off when the pressure at inlet exceeds the cracking pressure and allow the fluid to pass through the valve, as shown in figure 7. As, the pressure at inlet decreases less than the cracking pressure or there is any backflow in the system, the disc reverses its movement by the help of spring force and closes the valve opening. Instead of spring, gravity assisted disc movement is also incorporated in the valve sometime.
6. Swing Check Valve: ( Types of Check Valves )
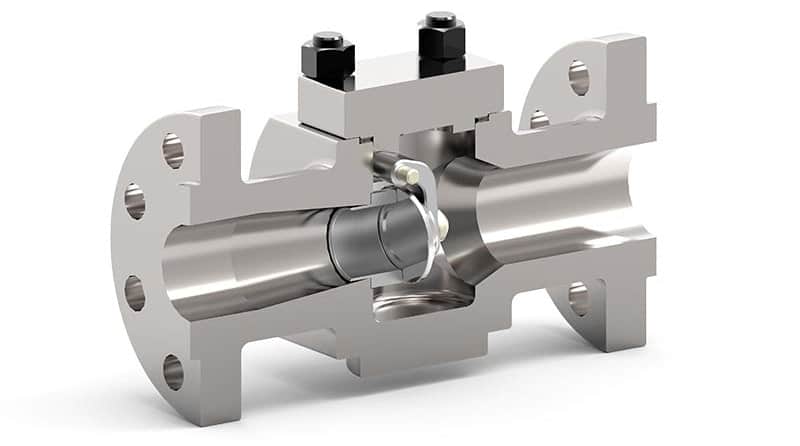
This check valve is also known as tilted disc check valve. It consists a disc that is hinged radially on one side. As the pressure at the valve inlet port increases, the disc swings about the hinge and opens the passage for fluid flow. In case of back flow, the disc swings back to initial position and completely closes the passage. There is no spring used in this valve and the movement of the disc is completely relies on the gravity. Figure 8 shows a swing check valve for instance.
7. Duckbill Check Valve: ( Types of Check Valves )
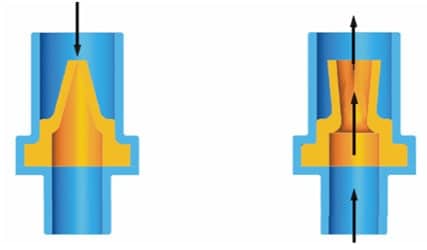
This check valve uses a soft tube that changes its shape according to the flow direction and hence, ensures the unidirectional flow of fluid inside the valve. If fluid is flowing in forward direction, the end of the soft tube changes its shape into diverging type and allowing the fluid to pass easily. As, the fluid reverses its direction, the end of the soft tube becomes converging and restricts the fluid to enter into it, see figure 9.
8. Wafer Check Valve: ( Types of Check Valves )
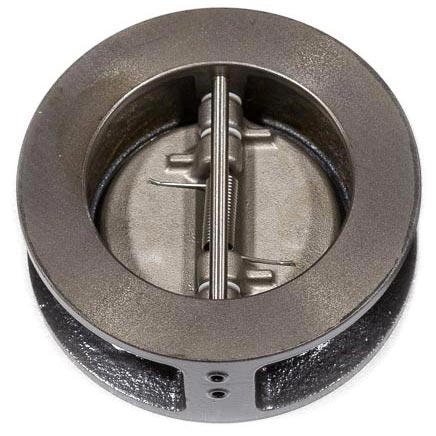
The wafer check valve consists of a wafer style disc that is hinged on one side, assisted with the spring, as seen in figure 10. If there is backflow occurs in the system, the wafer flips and cover the passage.
9. Stop Check Valve: ( Types of Check Valves )
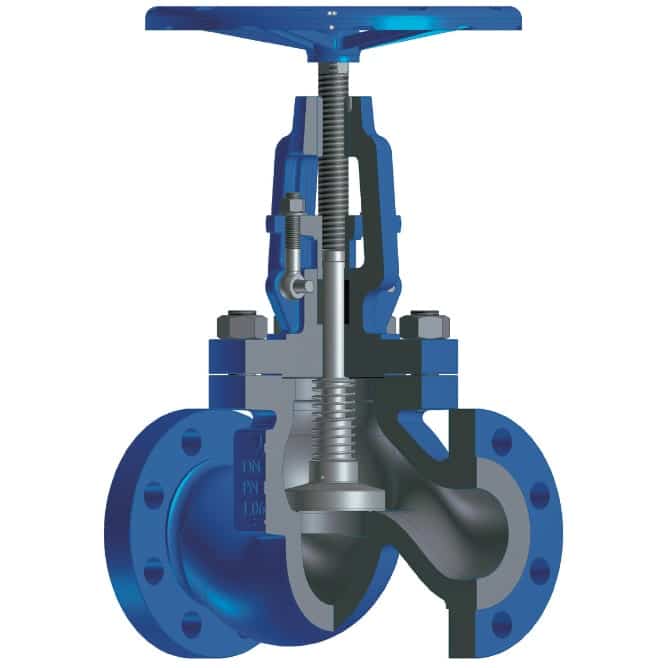
The stop check valve is basically a lift check valve or Y check valve with spring assistance. This valve has manual override feature which allows it to, apart from functioning as normal check valve, override and maintain the valve in open or closed state. Thus, this valve can be used for two features at a time. To perform the override actuation ids generally given by manually through a lever or wheel, as shown in figure 11. This type of valves is generally used in power generation plants, specifically in steam generators, turbines and safety accessories.
10. Foot Check Valve: ( Types of Check Valves )
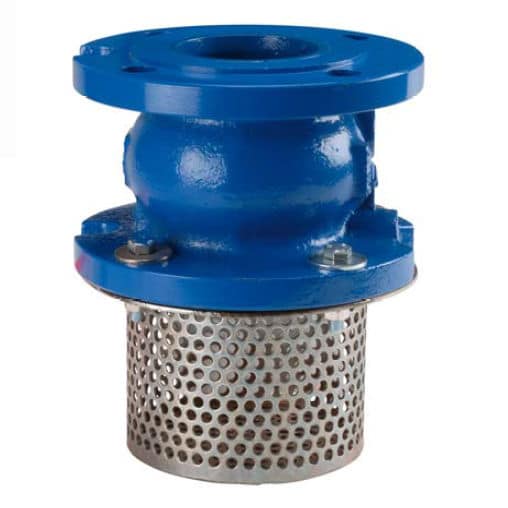
In this type of valve the inlet port is not available, instead, a strainer is available in place of the inlet port, as shown in figure 12. It is basically an in-line ball check valve with spring assistance. This helps the valve to maintain or allow the flow only in one direction whereas block the passage in reverse direction. The strainer available at the inlet prevents the debris and sand particles to enter into the check valve which may cause damage for the check valve as well as the fluid flow system. It is generally installed at the end of the pump suction line of a fluid flow system.
The materials used to manufacture the different types of check valves are generally stainless steel, brass, poly vinyl chloride (PVC), polypropylene (PP) etc. The selection of valve type and its materials depends upon following factors: –
- The compatibility of the material with the flowing fluid.
- Size of the pipeline and space available.
- Requirement of cracking pressure and reseal pressure.
- Installation direction; horizontal or vertical.
- The dimension and shape of the envelope.
- Accessibility for the inspection, maintenance and repair.
- Temperature of the flowing fluid as well as working environment.
Applications of Check Valve
On the basis of work function of the check valves, it can be used for following different applications;
- To prevent the backflow of fluid creating damage to the system.
- To ensure the prevention of contamination due to backflow of the fluid.
- To avoid the siphoning action in a pipeline.
- To maintain the vacuum seal.
No comments:
Post a Comment